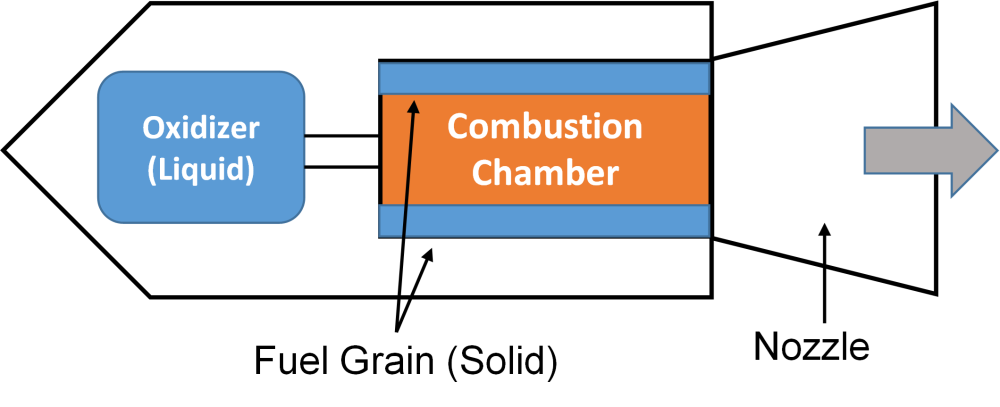
Figure 1. Schematic diagram of a hybrid rocket motors
As seen above, the solid fuel and the liquid propellants are separately stored. During ignition, the liquid oxidizer is pumped into the fuel chamber which also serves as the combustion chamber. Hot gases resulting from the fuel-oxidizer combustion are expelled from the nozzle, propelling the rocket forward.
Hybrid rockets have the following three major advantages:
- They are safe: Compared to solid rockets, in hybrids, the propellants are stored separately, reducing the probability of accidental ignition. Additionally, as compared to both solid and liquid rockets, hybrids can use more inert, and hence safer, fuels.
- They are cheap and simple: As opposed to liquid rockets, only one reactant is in the fluid state. Hence, the plumbing and pumping complexity and costs are halved for hybrids as compared to liquid motors.
- Their output can be throttled: By controlling the flow rate of the fluid oxidizer, the thrust level can be controlled, based on mission requirements. This capability is absent in solid motors since its combustion cannot be controlled post-ignition.
However, they suffer from two major drawbacks:
- They are difficult to ignite: Partly because hybrid propellants are more inert than solid and liquid rocket propellants, they are harder to ignite. Conventional hybrid rocket ignition systems either (like a heating element or plasma-arc igniters) add weight and complexity to the system or degrade over time (like catalytic igniters), compromising re-ignition capabilities.
- They suffer from lower regression rates: The regression rate (and hence, thrust per given size of motor) of hybrids is atleast an order of magnitude lower than solid rocket motors. This leads to increased size and greater weight or more atmospheric drag.
Overall, the project’s focus is to research hypergolic propellants and understand their performance with a view to eventually use them in hybrid rockets to overcome the drawbacks of conventional ignition systems. Hypergolic propellants are those that ignite upon contact without the need for external heat/energy sources. They solve ignition problems by firstly removing the need for a separate, intricate ignition system and secondly by ensuring great re-ignition capabilities. Conventional hypergolic propellants like MMH (monomethyl hydrazine) and RFNA (Red fuming nitric acid) are toxic: this research focuses on studying a promising class of non-toxic or “green” hypergolic hybrid rocket propellants.
The project is currently focusing on a propellant consisting of Rocket Grade Hydrogen Peroxide (RGHP) as oxidizer, polyethylene (HDPE) as fuel and sodium borohydride or SBH (NaBH4) as an energetic additive embedded in the HDPE fuel matrix. Figure 2 below shows the ignition progress with this propellant.
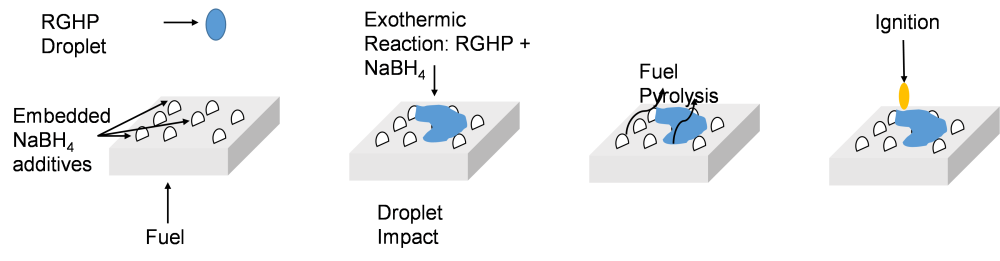
Figure 2. Ignition process for RGHP-HDPE-SBH propellant
As shown in the picture above, ignition proceeds when the RGHP droplet impinges on the solid surface. After impact, the liquid RGHP undergoes a rapid exothermic reaction with the exposed SBH particles on the fuel sample surface. The heat release pyrolyzes the HDPE fuel. This heat also provides the energy required for igniting the flammable pyrolysis products, with combustion proceeding in the gas-phase. Thus, ignition is achieved without the need for a separate igniter; the ignition system is “built into” the reactants.
Figure 3 shows ignition of the HDPE + SBH fuel with just one drop of hydrogen peroxide.
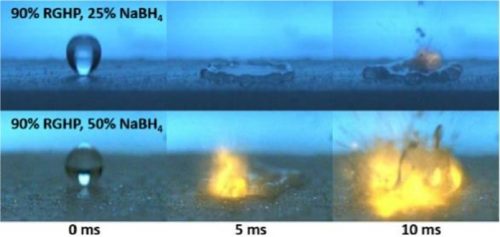
Figure 3. Ignition of fuel with one drop of oxidizer
As can be seen in the above figure, ignition is rapid and energetic with the entire ignition event wrapping up in less than 10ms. For hypergolic propellants, fast ignition is important; in a real hypergolic hybrid rocket motor, slow ignition can cause propellants to accumulate in the combustion chamber which can simultaneously ignite, causing undesirable pressure spikes. In general, faster ignition is generally desired also because in applications like satellite propulsion, quick ignition and re-ignition implies accurate positioning and maneuvering.