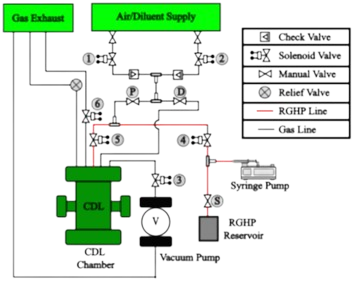
The experiment consisted of spraying RGHP from a nozzle situated vertically above the fuel sample within a stainless-steel chamber, with the gas and oxidizer flow remotely controlled by solenoid valves to regulate both the oxidizer delivery and the composition of the diluent gas, as shown in Figure 1. After each ignition, the chamber was purged with and then depressurized to atmospheric conditions, allowing for a restart and the repetition of the experiment.
The Chamber has four sapphire window viewports, allowing optical access both in the infrared and visible wavelengths. The imaging setup for the work involved using three cameras placed adjacent to the three viewports with a powerful DC LED light placed adjacent to the remaining window. The imaging setup for the experiment is shown in the following figure.
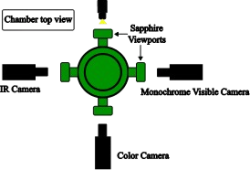
The infrared camera was the Telops FAST M3K and the monochrome visible imaging camera was the Photron SE-Z. Both these cameras provided optical access in the infrared and visible imaging ranges, respectively, and were set at an image acquisition rate of 2000 frames per second. The IR camera, in conjunction with an attached optical filter, could also detect species like water, CO2 and hydrocarbons from the ignition event. The third camera was a color camera (Phantom V310), which imaged at a rate of 200 frames per second and was utilized to provide contextual imaging of the droplet impingement and spray ignition event; the color images allowed for better imaging of the droplet impingement and combustion process.