Student Design Project – TechAway Design/Build/Fly Contest
- O. Goldbaum, R. Pryluk, R. Dvorkin, R. Tsalik, D. Matalon, M. Yeger, A. Salomon, V. Katz , A. Peker, R. Abramovich
- Shlomo Tsach
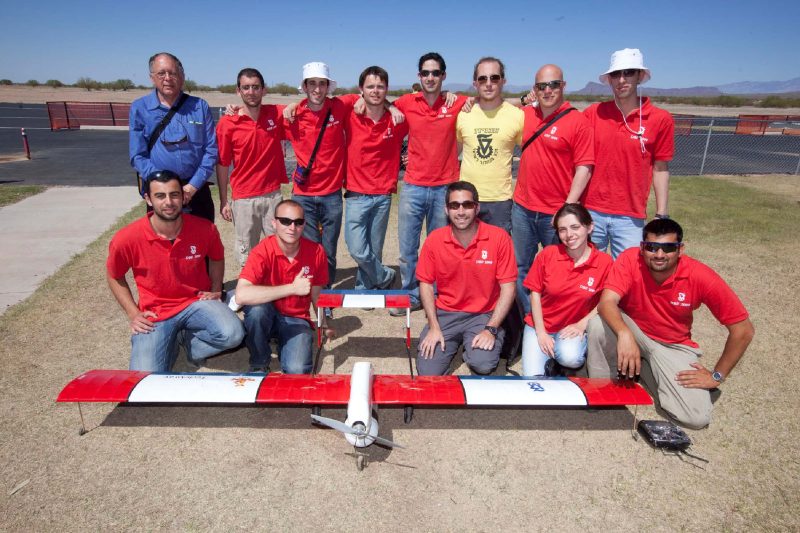
Tech-Away, the Technion – Israel Institute of Technology’s entry in the 2008-2009 AIAA Design/Build/Fly competition, in Tucson, Az. The goal of the design was to maximize the competition score, which is a combination of the report score and total flight score. The Tech-Away project required a student design group with extensive knowledge in aircraft design and a skilled manufacturing group, together with capabilities of aerospace project integration and management, for a complete successful team.
In order to have the aircraft ready and perfected in time for the contest, the processes of designing and building were divided into three phases: conceptual design, preliminary design, and detailed design.
During the conceptual design phase, several wing and fuselage configurations were considered — conventional wing, tandem, canard, and flying wing. The fuselage configurations considered were conventional fuselage, boom mounted and dual boom. In addition, propulsion, landing gear, battery configurations and box configuration were discussed. A figure of merit (FOM) analysis resulted in selecting a conventional wing along with a dual boom fuselage for S&C, a single-tractor propeller with bronco tail, tricycle landing gear for ground handling, a single battery pack and a single large box.
Aerodynamic and propulsion optimizations were conducted to maximize the flight score. The aerodynamic parameters included wing span, chord, wing area, airfoil selection, horizontal and vertical tail area and profiles and elevator and rudder sizing. The propulsion parameters included motor and propeller selection, and battery optimization. The wing span was optimized to 9.908 ft, the chord was 0.82 ft and the rectangle wing area was set to 8.1245 ft2 with an AR of12.08 and a FX 63-137 airfoil. For the vertical tail (VT) and the horizontal tail (HT), a span of 0.754 / 1.903 ft and an area of 1.134 / 1.748 ft2 with a NACA 0009 / 0012 airfoils were set. In addition, the VT / HT volume coefficient were optimized to 0.038 / 0.625 and the rudder / elevator size was set at 22.7% / 29% of the VT / HT area. The propulsion optimization offers a Neo 15091.5Y motor: 1:6.7 geared is the most efficient for all three missions. A 17×13 propeller with an Elite 1500 cells produces the highest score for Mission #1; for Mission #2 and Mission #3, a 20×12 propeller with an Elite 2000 cell, and a 19×10 propeller with an Elite 1700 cell, respectively, are the most efficient and performed optimally.
The following performance capabilities were predicted in order to evaluate the expected flight score for Mission #1, Mission #2 and Mission #3: Takeoff distance of 12/ 90 / 75 ft, a cruise speed of 36 / 55 / 46 ft/s, a stall speed of 26.2 / 38.6/ 33.2 ft/s and a maximum speed of 82 / 105 / 96 ft/s. The assembly time and loading time were estimated at 15 and 8 seconds. The total RAC is 29.25 lb, the estimated AT is 15 seconds which yields SCF of 0.002228 [1/ (lb∙sec)].
The team was placed 16th out of fifty teams which competed.
Links: http://www.aiaadbf.org/2009_files/aiaadbf.htm