A3TB – Year III
- Oren Montgomery, Jenia Grichanovsky, Guy Gordon Biberstein, Yishay Glam, Matan Winter, Saber Boulahjar, Amit Gabay (Team leader)
- Dr. Lucy Edery-Azulay
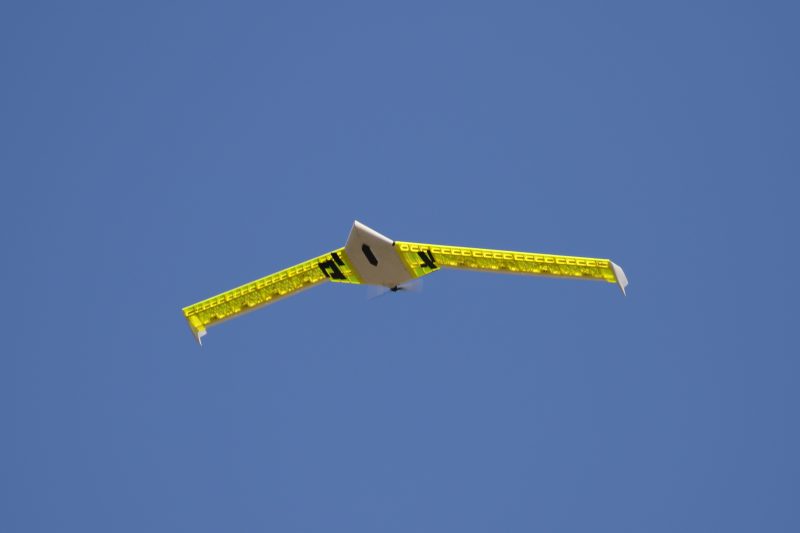
Intro
The project engages in the design, development, and production of an aeroelastic technology demonstrator for future research of aeroelastic. The project is of a flying wing configuration, propelled by an electric motor. The airplane’s structure is inherently flexible, being 3D printed out of Nylon-12 polymer. The airplane utilizes a proprietary design automatic control system for stabilized flight. The airplane was flight tested, and the results validated all of the analytical model validation conducted as part of the design process.
Description
The project engages in the design, development and production of an aeroelastic technology demonstrator for future research of aeroelastics.
Project motivation: the aspiration for energy efficient aircraft (long range-low fuel consumption) leads to high aspect ratio and low weight wing configuration design. These configurations are more flexible than more conventional wing designs, these being heavier due to stiffening efforts. Thus, design of more flexible aircraft allows for weight reduction. Moreover, the utilization of a multiple control surface design adds more degrees of freedom for the control system, enabling future design of optimal performance control system.
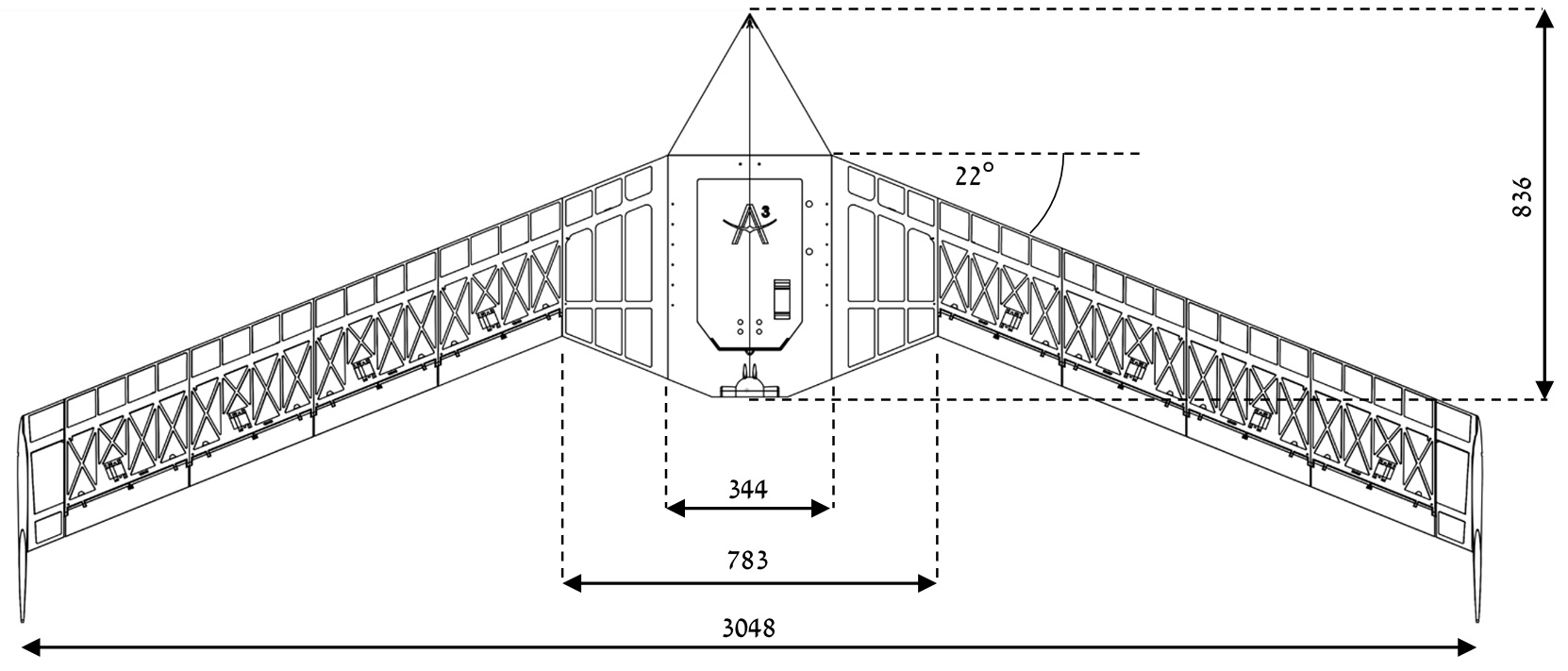
The flexible wing design results in a flutter speed purposely included inside the flight envelope, as a project objective. This, being one of the main challenges of the project, has matured to be one of its greatest achievements. The final test flight presented the final design product, a flexible flying wing demonstrating 3 major flutter events, matching all pre-flight analyses in regards of flying conditions.
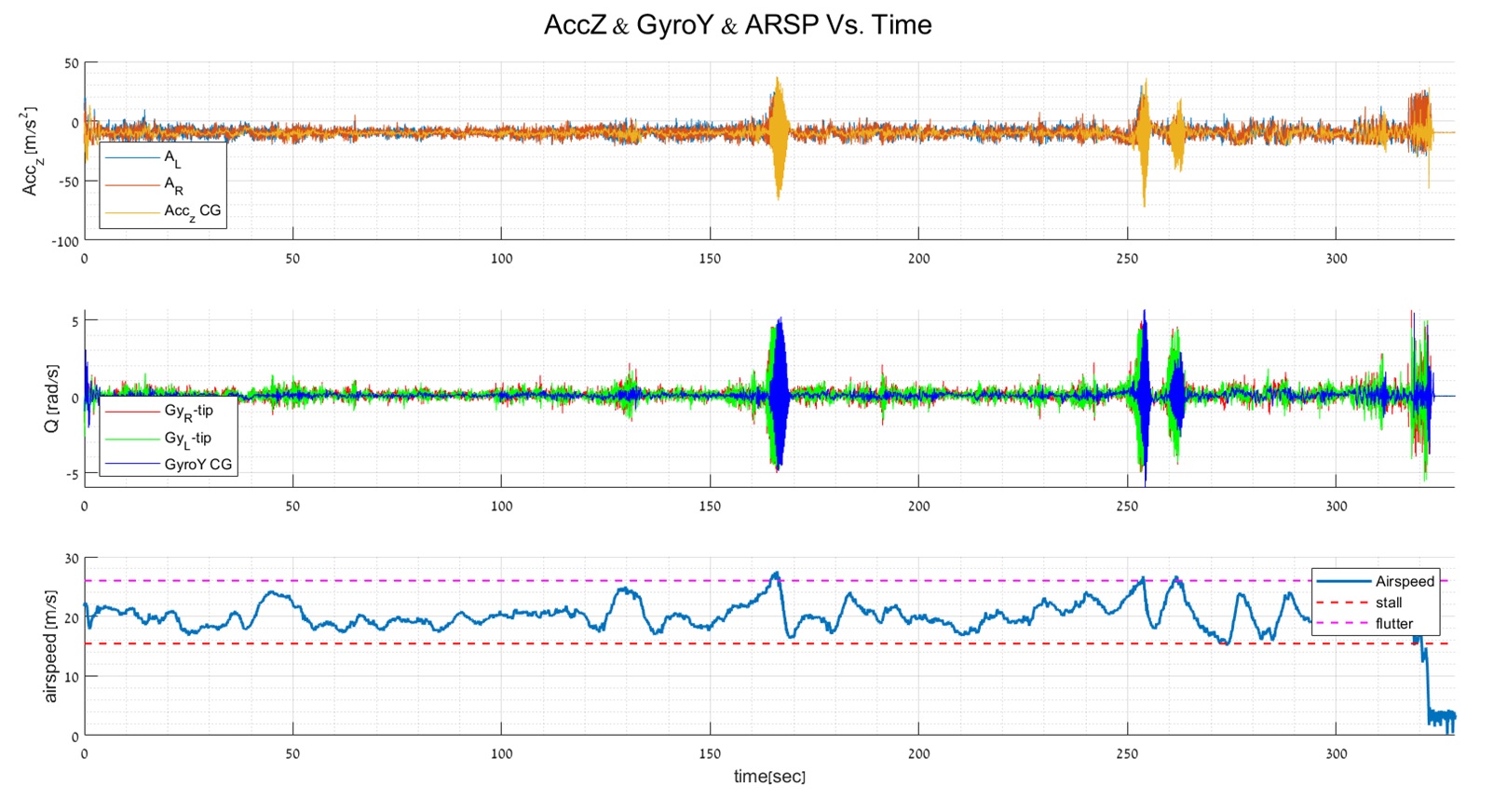
The project was planned as a 3-year project, this being it’s 3rd and last. The project’s main produce:
- A flexible, flying-wing configured UAV, manufactured in an advanced manufacturing method, enabling high complexity aeroelastic experiments to be conducted in a low cost and a safe manner.
- Fully functioning flight simulator, used for flight characteristics prediction, lowering the risks and managing resources.
- Ground Vibration Test (GVT) system, based on infra-red tracking cameras.
- Wing shape control infrastructure, utilizing it’s flexibility and multiple control surfaces.
- Computational model-based design process (structural, aerodynamic, aeroelastic) with high trust level, validated with lab and flight tests. Those models are supplied with the aircraft and are calibrated according to flight experiment results. Those will be used in future aeroelastic technology research.
- A 3-part document detailing the 3-year design process. Those parts describe the project requirements, characterization and design of the system and its components, configuration justification through computations and lab experiments, flight experiment information and debriefs and future recommendations.
In addition to this project being in the forefront of aeroelastic research, it has been a major opportunity for the students to learn and have a hands-on experience in advanced and industry practical domains: 3D printing oriented design, processes involving complying with ICAA requirements for UAV operations, preliminary flight readiness reviews, formalizing the relations between the aerospace faculty and civil airstrips and more.
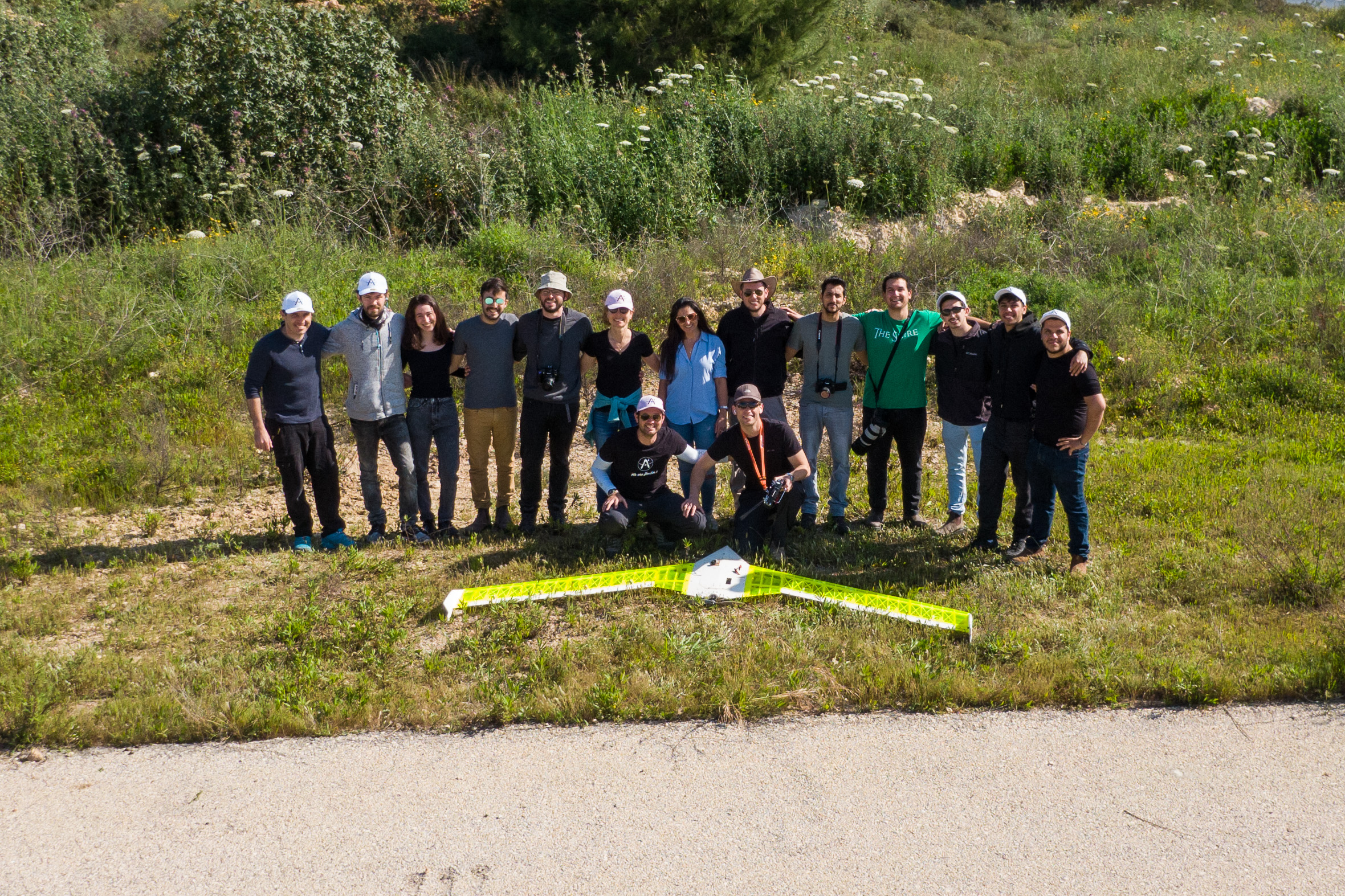