Cornetto Project 2020
- Noa Kadosh, Eden Yanko, Eytan Podvalni, Noam Mansano, Max Elman, Daniel Benaroya, Ilanit Ifergan, Shmuel Cern.
- Shlomo Shpund, Roman Gandelman
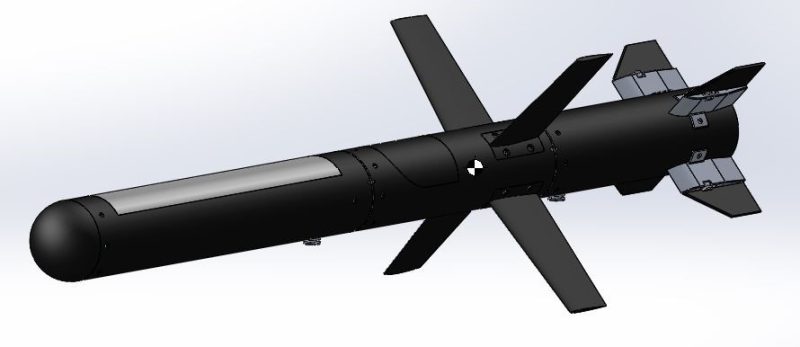
Design, Build and test an educational experimental missile for research, test and demonstration of missile technologies.
Missile’s reference missions:
- Perform a roll-controlled ballistic trajectory, reaching a maximal height of 1500 [m]. The missile will be recovered on its way down by a parachute.
- Perform a designed trajectory combined of roll-controlled ballistic and glide trajectory. The missile will be launched to a ballistic trajectory and start a glide maneuver at a predetermined altitude. The flight conditions will be optimized for the missile to achieve a maximal range.
The missile comprises 3 sections: Avionics (contains the flight computer, battery, telemetry etc.), Recovery (parachute and deploying mechanism) & Aft section (wings, flight control unit and rocket motor. The flight control unit mounted at the aft enf of the missile and contains 4 servo actuators actuators and aero. fins.
Throughout this year, we have been working in the following fields:
- System engineering
- Detailed structural design
- Avionics assembly
- Flight control
- System Simulation
The main goal in this year, was to get prepared and perform a launching experiment to demonstrate the first mission. From previous year we received a preliminary structure design, built control loops and 6DOF simulation. We upgraded their design and simulation according to our new ideas and requirements.
During the winter semester, the structure model was improved, and detailed design was carried out. Meanwhile, connections with different manufacturers were created, to get professional advice for production possibilities of main structure parts. With the help of those, we chose materials for each structural element, designed the connections between the missile’s sections, and finally reached a final detailed design model, ready for manufacturing. Afterwards, we contacted with
different manufacturers to receive bids for production.
Work was done also in the control and simulation field: the 6DOF simulation was debugged and updated, an aerodynamic configuration was chosen based on the ballistic trajectory simulation, and the thrust model evaluation of our two potential propellants was done. Different types of uncertainties were defined and modeled in the simulation, such as mass changing, environment conditions, aerodynamic coefficients errors, wind effect, non-axial thrust, various launching angles etc. According to those, “Monte Carlo” simulations were performed, to evaluate the “footprint”of the hit-points of the missile on the ground. In the control field, we developed an automatic method to calculate the gains of the control loops according to design requirements (such as gain and phase margins, settling time, etc.).
During the spring semester, the main mission was to perform a launching experiment to demonstrate the ballistic roll-controlled trajectory. Unfortunately, the original goals could not be performed due to the unexpected spreading of the Coronavirus. Most of our original plans were related to manufacturing of missile structural parts, lab experiments and abroad suppliers, but the circumstances of the difficult situation could not afford any of those.
Thus, an alternative work plan was established and carried out. We decided to focus on the avionic section assembly, which was not fully developed. The avionic plate was reorganized, detailed design of the section and the electric circuits of the missile was done. We created an “Ironbird”, which resembles the electrical connections in the missile and ensures the functioning of each component. The recovery mechanism of the missile was fully developed, a dynamic analysis was done
and the whole section was modeled in detail.
As for the control and simulation field, validations of the control loops were made, and the loops were tested under different types of launching conditions. According to the demands, the simulation was transformed into the discrete world so it will illustrate the real world, the drag model of the missile was extended and modeled in the Transonic flight Regime. Servo experiments controlled by the flight computer were performed in the control lab to exercise the use of the integrated system, document its performances and model its transfer function, for the integration in the simulation and flight control advanced design.