Eagle’s Wings – Air Launch Platform for Micro-satellites
- Benny Begun, Eran Ben-Shimon, Itay Farajun, Mira Tal, Omer Weizman, Orel Portal, Oren Fischman, Sapir Amsalem, Sefi Klingel, Shay Renzer
- Dr. Micha Boasson
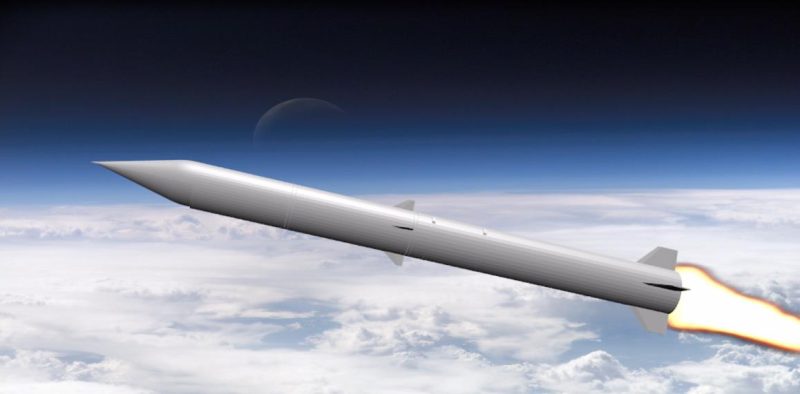
Eagle’s Wings is a Micro-Satellites Air launch vehicle designed by a team of students in the Technion. The project’s goal is creating a system that enables launching and orbit insertion for micro-satellite using an airborne aircraft.
Air-launching is an evolving area that researched and tested by aerospace companies such as NASA, DARPA, Lockheed Martin,among others..
The motivation is clear: since ground launch demands large fuel tanks, expensive launch system and has significant dependence on the launch condition (weather and location on earth) – air launch can become a strong alternative.
Hence, this project gives an option for mobile, fuel-saving, much smaller and with higher availability micro-satellites launch system.
System requirements
The design needed to fulfill the following requirement:
- Enabling launch from flying aircraft.
- Carrying Satellite with maximum weight of 50 kg.
- Orbit insertion at 250km ± 2% above earth.
- Can be carried by Israel Air Force aircraft F-15I.
- Can be carried by other types of aircraft (for commercial purposes).
Design
Inside each of the three stages of the launcher, a solid fuel engine was installed – in order to provide the required thrust for the mission. Unique, very small hydrazine engines are planned for the last stage – enabling more accurate control for the orbit insertion. The propellant takes 85% from the total 3,115 kg rocket mass. The propellant compound was chosen to provide the highest specific impulse and thrust given the geometric constraints.
Trajectory calculations were performed by numerical simulation to ensure precise tracking of the rocket’s path and so that the stage leftovers (from the separations) will fall onto Earth in unpopulated areas. The trajectory was calculated using a 6DoF simulation over 7 state variables (additional one for mass). The simulation includes precise gravity and atmospheric models, along with accurate calculations based on the missile’s body and aerodynamic configurations and in-depth engine and combustion chamber geometries. In addition, to ensure that the missile will follow the correct given path, even in non-ideal dynamics and under perturbations, a missile flight control system was designed and a method for trajectory guidance was overviewed.
A special consideration was made to reduce the system weight and make it easier for carrying. By stress analysis, a decision was made to use composite material (Kevlar epoxy) for the engine tanks and aluminum 229-1T81 for the rocket structure. Separation rings were designed to ensure safe and timed separation. Hangers, that connect the rocket to the aircraft, were planned to add minimum drag and weight to the system.
For yielding a controllable system – there was a need for aerodynamic analysis and steering panels design. Using analytic calculation, Missile Datcom program and CFD simulation for comparison – a 4 steering panels were installed on the tail of the first stage, and other smaller panels were installed on the end of the second rocket’s stage – both designed for supersonic flight. A wind tunnel model (printed by 3D printer) was tested at the faculty’s wind tunnel and the control problem was solved by the hydrazine engines.
Finally, based on simulations, the requirements can be fulfilled with the proposed design.In other words – the project ‘Eagle’s Wings’ succeeded to design an air launch platform for micro-satellites.